圓錐破碎機(jī)的9大常見(jiàn)故障及解決方案:
1、油壓、油溫異常
(1)、過(guò)濾器堵塞時(shí),其前后油管油壓不同,若油壓差>0.04MPa,可先不經(jīng)過(guò)濾器供油,再拆洗過(guò)濾器,但直接向破碎機(jī)供油應(yīng)小于2-3h;
(2)、油溫低,油開(kāi)關(guān)未開(kāi)好,油泵運(yùn)轉(zhuǎn)不良時(shí),會(huì)引起油量指示器內(nèi)無(wú)油流,油泵雖運(yùn)轉(zhuǎn),但油壓<0.05MPa,需加熱油、開(kāi)好油開(kāi)關(guān),檢修或更換油泵;
(3)、冬季油溫太低,an全閥失靈或泵油能力太大,給油壓力過(guò)大時(shí),會(huì)使破碎圓錐被抬起,應(yīng)加熱油、調(diào)整an全閥或更換油泵;
2、圓錐破電流過(guò)高
大型圓錐破給礦過(guò)多、不均、含粉礦過(guò)多或潮濕,應(yīng)調(diào)整設(shè)備均勻連續(xù)給礦,給礦前清除含粉礦過(guò)多的礦石;潤(rùn)滑不良時(shí),需拆檢、潤(rùn)滑運(yùn)動(dòng)部件;軸承或球面軸承損壞時(shí),需更換備件;
3、圓錐襯板磨損失效
大型圓錐破轉(zhuǎn)速高、破碎力大,壓縮、剪切壓力巨大,圓錐襯板易發(fā)生切削、塑變和疲勞等磨損失效形式,產(chǎn)生復(fù)塑性變形、疲勞裂紋剝落等,損耗量大。
4、圓錐破碎機(jī)“飛車(chē)”
故障原因:軸襯內(nèi)壁刮研不良、裝配不當(dāng)或磨損過(guò)甚;破碎機(jī)運(yùn)行磨合不充分,主軸與軸襯之間潤(rùn)滑油膜強(qiáng)度不足;軸襯與主軸配合良好,但動(dòng)錐球面與碗形軸承磨損;
解決辦法:保障錐套內(nèi)外孔裝配間隙,保障主軸和錐套沿全長(zhǎng)接觸,錐套與軸心套須用融化的鋅合金固定,以確認(rèn)二者之間無(wú)任何相對(duì)運(yùn)動(dòng)。
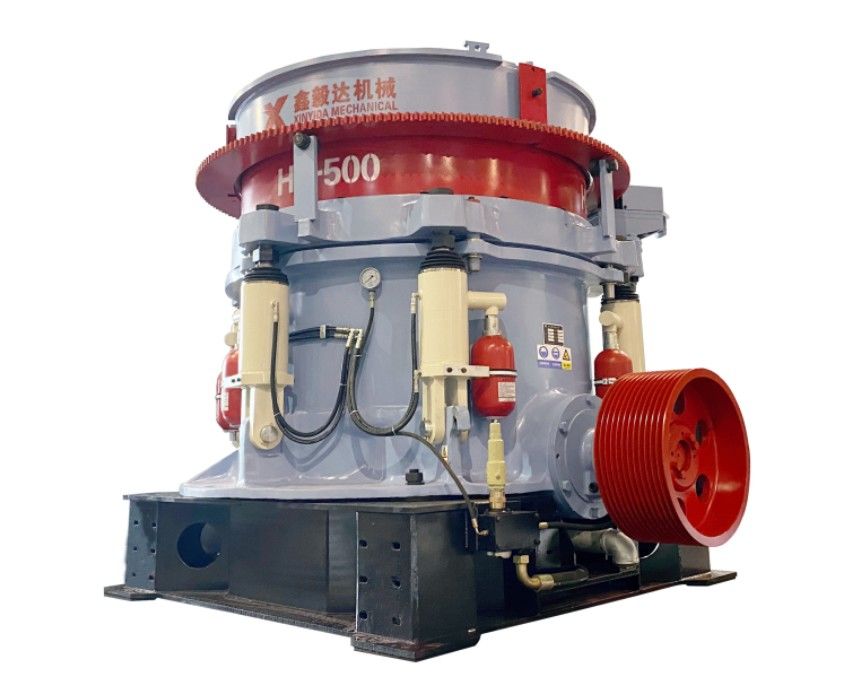
5、錐齒磨損過(guò)甚、打齒
故障主因:保護(hù)裝置不完整;喂入渣鐵物料超過(guò)設(shè)備過(guò)鐵大尺寸而被卡死;圓錐破被堵停機(jī),帶重負(fù)載強(qiáng)行啟動(dòng);配置傳動(dòng)電機(jī)不匹配,嚴(yán)重影響效率和設(shè)備正常運(yùn)行。
解決辦法:設(shè)計(jì)兩道除鐵,除原有喂入渣料皮帶頭輪除鐵外,在喂入渣料的皮帶上增設(shè)永磁吊掛除鐵裝置,可有效避免渣鐵混入破碎腔;月檢發(fā)現(xiàn)液壓油箱內(nèi)部的金屬含量超標(biāo)時(shí),需及時(shí)處理;完備操作制度,加強(qiáng)對(duì)破碎機(jī)過(guò)鐵的監(jiān)管和連帶責(zé)任考核,可提高機(jī)器作業(yè)效率和使用壽命,大幅降低運(yùn)行成本。
6、調(diào)整環(huán)跳動(dòng)頻繁
要嚴(yán)格控制入料粒度,防止非破碎物混入破碎腔內(nèi);要鎖緊調(diào)整帽;啟動(dòng)圓錐破前,需多方位排查,確認(rèn)調(diào)整環(huán)、鎖緊環(huán)螺紋的間隙合理,增加鎖緊行程,減少調(diào)整環(huán)、鎖緊環(huán)螺紋和鎖緊螺栓的磨損;給礦漏斗設(shè)計(jì)非常重要,應(yīng)*落料中心盡量靠近破碎機(jī)中xin;
7、過(guò)鐵及瞬時(shí)悶車(chē)
一旦過(guò)鐵及瞬時(shí)悶車(chē),其液壓自動(dòng)過(guò)鐵能液壓起頂、自動(dòng)排料,使鐵塊通過(guò)破碎腔;為保險(xiǎn)起見(jiàn),應(yīng)增設(shè)金屬探測(cè)儀,并使之保持靈敏可靠的狀態(tài),可實(shí)時(shí)監(jiān)測(cè)過(guò)鐵狀況,避免因過(guò)鐵卡死而停機(jī)。
8、潤(rùn)滑油失效
定期檢查迷宮密封;超過(guò)使用周期2000h后,潤(rùn)滑油粘度等指標(biāo)會(huì)驟降,須定期更換。
9、破碎機(jī)振動(dòng)過(guò)大
應(yīng)正確給料,將排料口調(diào)整在允許范圍內(nèi),減少進(jìn)料中的細(xì)料和粘性物料,按規(guī)定扭緊彈簧上壓緊螺母或更換彈簧;
圓錐軀體下沉?xí)r,引起破碎機(jī)強(qiáng)烈振動(dòng),破碎圓錐部自轉(zhuǎn)很高,應(yīng)拆檢或更換襯套、主軸等,排查缺油原因并消除;合理調(diào)整襯套間隙;重新刮研且達(dá)到要求。
免責(zé)聲明:文章來(lái)源于網(wǎng)絡(luò),不代表本站觀點(diǎn),內(nèi)容版權(quán)歸屬原作者及站點(diǎn)所有,如有對(duì)您造成影響,請(qǐng)及時(shí)聯(lián)系我們予以刪除!